Talking TPMS – Know How it Works, Then Know What to Say!
March 22, 2022
Scot Holloway, CEO - Bartec USA
We all know that servicing Tire Pressure Monitoring Systems can be challenging. It can even be harder explaining TPMS to consumers. The good news is there are steps that can be taken to make the process of Talking TPMS easier, more effective, and as a result even produce more opportunities to sell parts and service. It always helps to have a plan, so here's an example.
Talking TPMS begins with Education. Yep, it's on the front counter professional to educate themselves on what Tire Pressure Monitoring is all about. The components, the function, and the pitfalls and the risks if you ignore proper preventive maintenance. Consumers, by and large, are looking for the expert advice from their auto care professionals, the front counter professional needs to seize the opportunity and become that expert!

Direct TPMS has five basic components:
- Wheel Sensor
- MIL/TPMS light
- Antenna
- Control Module
- Placard Label
In the majority of cases, the technician will focus on the sensor in the wheel, the status of the MIL/TPMS light, and the Placard. The placard shows the Recommended Inflation Pressure [RIP] for the vehicle for the wheels and tires on the vehicle. Note: it is a best practice to always confirm that the vehicle does in fact have fitted, the wheels and tires that are specified on the placard. Up-fitting and plus sizing can impact load carry capacity and recommended inflation pressure, so know the vehicle setup! If a vehicle has custom wheels and tires, and TPMS, verify that the custom setup supports the vehicle per the stock RIP. If the RIP has changed, the TPMS should have been recalibrated and a NEW supplemental placard label attached adjacent to the OE label.
After verifying the placard, the focus moves to the Malfunction Indicator Light [MIL]. With the Key On Engine Off [KOEO] look at the instrument panel and whether or not the MIL is on solid or flashing. A solid light means a low-pressure condition in one or more of the tires. A flashing MIL means a system problem, and further diagnosis by the front counter professional or the technician is required.
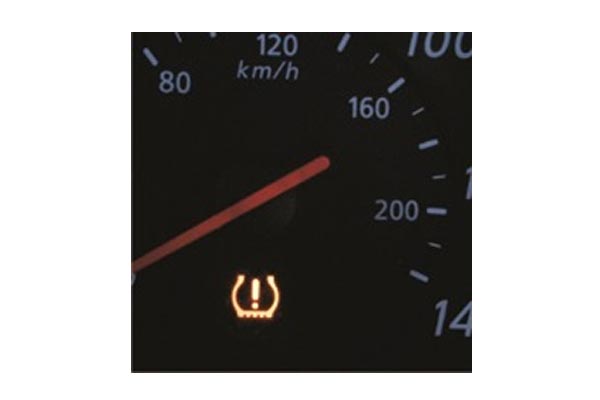
Understanding the most common TPMS issues is critical. In MOST cases, TPMS issues are related to the sensor either not functioning, not properly relearned to the vehicle, is missing, or is in the incorrect position [not relearned after a tire rotation]. Using the proper TPMS tool that can test for these scenarios, then display the information in an intuitive report is the accurate and fast way to get your customer’s TPMS issues resolved.
It's important to note that the in the cases of a nonfunctioning, not relearned or missing TPMS sensor, the TPMS MIL may not be evident. In other words, it can sometimes take a long while before a failed or missing TPMS sensor actually shows as a TPMS MIL [flashing light]. This makes 'Test Before you Touch' an absolutely necessity. This table summarizes typical TPMS sensor failure scenarios.

Once you've mastered the basic understanding of how a TPMS functions, and the components that comprise a TPMS, you are well on your way to TALKING TPMS with the customer. Perhaps the single most important tool at the disposal of the front counter professional or technician is the TPMS inspection report. If you can collect all of the relative data from the customer’s vehicle, you essentially have the makings of a SCRIPT of what can should be discussed.
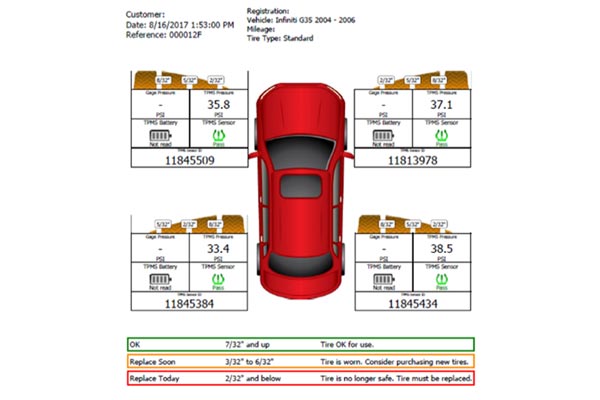
This is a typical TPMS inspection report that is available from today’s TPMS tools. Notice the details with which can be discussed with the consumer. In this instance, the front counter professional has enough data to discuss the wear of the tires, current tire pressure [an indication of whether or not the tire have been maintained], the amount of remaining tread, and of course the condition of the four TPMS sensors. Many reports like this also contain additional data like Diagnostic Trouble Codes [DTC’s] detected from the vehicle control modules.
Using an inspection report like the one shown, provides loads of information that can be used to inform, educate, and in many ways keep safe your customers. To further understand and better diagnose these scenarios, look to the TPMS inspection report. For example, in the case of a nonfunctioning sensor, the inspection report my look like the following sample:
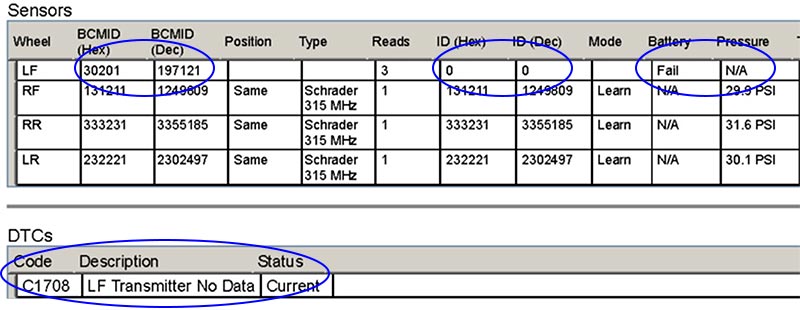
Note that for wheel position Left Front [LF], there are zeros for the ID’s as read by the tool. You can also note the ID’s that are still registered [or stored] in the Body Control Module [BCMID]. This information combined with the corresponding Diagnostic Trouble Code [DTC] is the exact type of information that should be shared with your customer as you walk them through the diagnosis.
Another common scenario is the TPMS Sensor not relearned to the control module. Your customer arrives with a TPMS MIL [flashing light]. You get your TPMS tool our and Test Before Touch, however you find that despite the presence of a MIL, all of the sensors are functioning properly and are the right parts for the vehicle.. Here comes the importance for the ability to connect via the OBDII port and to quote a famous radio personality, 'Get the REST of the story!'
The following data can be found simply by reading the stored information [in the BCM] and comparing it to what was tested or read by the tool. In the case of the un-relearned system, the inspection report might look like the following:
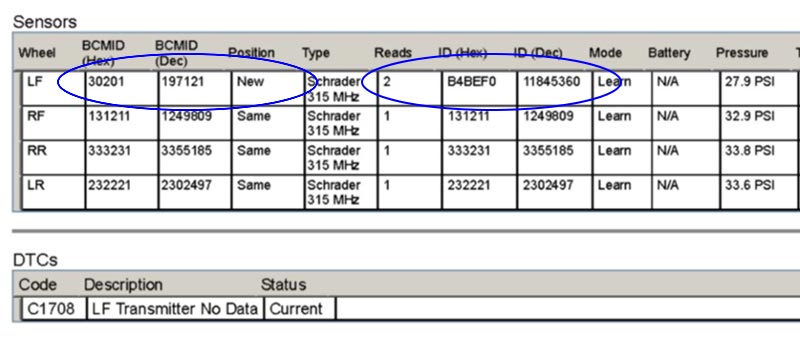
Note that the sensor installed in the Left Front position, while functioning, is NEW. You will also see that the sensor ID as read by the tool does NOT match what is stored in the control module. This would explain the TPMS MIL the customer is experiencing. This would also point you in the direction of an easy solution. Simply perform a TPMS relearn, which will write the correct Sensor ID, and clear the corresponding DTC.
These are just but a few examples of how having more detailed information can only improve how you talk TPMS with customers. As the old saying goes, knowledge is power. Have a plan and make sure technicians are educated in the workings of Tire Pressure Monitoring Systems. TPMS is an important safety system that requires checking and maintenance.
Front counter associates and technicians that are armed with knowledge and a plan for informing customers can be successful in keeping their customers safe. Talking TPMS however, requires practice of that knowledge and a commitment to become an expert. To successfully talk TPMS, there are a few things to a front counter professional must commit to knowing, but with time they can effectively manage these discussions with their customers. It is worth noting that a key resource for any tire store is their TPMS Parts Provider. Companies that provide sensors, service kits and the necessary tools, should be equipped to provide the support needed.
Other Articles
Another Great Day At SEMA Garage Detroit
September 2, 2025
Happy Labor Day 2025 From Bartec TPMS
September 1, 2025
Limited Time Offer From Bartec TPMS
August 28, 2025
Your #1 TPMS Partner Come & See Us at SEMA 2025
August 22, 2025
Get More With Bartec TPMS TECH550Pro Bundle Deals
August 19, 2025
Get More With Bartec TPMS TECH600Pro Bundle Deals
August 18, 2025
Rite-Sensor® In Stock Ready To Ship
August 14, 2025
Limited TPMS Bundle Deal Available
August 11, 2025
Industry Leaders in TPMS Expertise
August 8, 2025
99.9 Percent TPMS Sensor Coverage
August 4, 2025